
EXPERIENCE
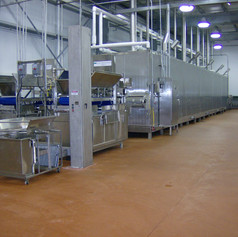

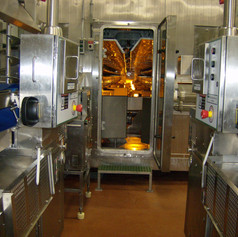
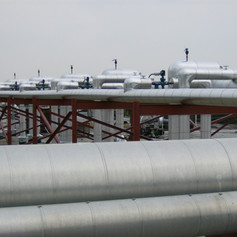
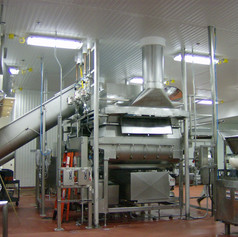


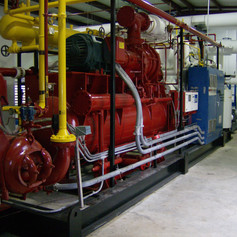

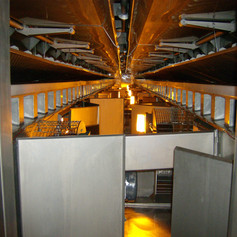
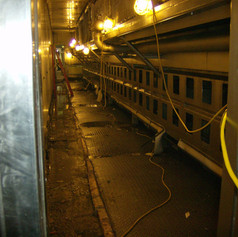
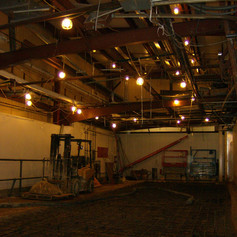
Management
-
Managed Engineering and Maintenance Functions for a seven-facility $1 Billion Meat Producer completing over 130 Capital Projects in just under five years.
-
Directed the Maintenance and Capital Budgets for a $1 Billion Food Producer with MRO Budgets of $8 Million per year and Capital Budgets of $5 Million per year
-
Planned, Initiated and Completed Capital Projects up to $9 Million in size with extremely tight time frames critical to Production
-
In charge of Plant Engineering and Maintenance Management for 350,000 sq ft Pork slaughter facility with a Capital Projects Budget of $3.5 Million, Repair Projects Budget of $1.9 Million, and MRO Budget of $3.8 million.
-
In charge of Plant Engineering and Maintenance Management for two potato product processing facilities with $13 MM budget for MRO and Capital Projects
-
In charge of Plant Engineering and Maintenance Management for three meat product facilities with $11 MM budget for MRO and Capital Projects.
-
Reduction in Plant Maintenance Downtime of 40.37%.
-
Reduction of 75% in Engineering Department Maintenance personnel turnover.
-
Establish SPC measurement tools and data tracking for downtime.
-
Establish budgets for Capital Projects, Repair Maintenance Accounts, Project and Scheduling.
-
Establish positive counseling and communication with Engineering Team including Counseling Forms, Progress Records and Measurement Tools.
-
Complete planning and budget for reducing maintenance expenses by 10% annually. Goal reached.
-
Established a system of Repair Accounts for budgeting major repair expenses on an annual basis.
-
Created and implemented Three-year State Certified Maintenance Technical Training Program.
-
Completed Tennessee Associates training to become a proficient Total Quality Management Facilitator.
-
Train and develop the facility Natural Management Team for the initiation of TQM in the plant processes.
-
Planned and directed Contractor Safety Seminar in preparation for Annual Maintenance Shut-Down.
-
Implement MUSCLE computerized maintenance system for the facility.
-
Implemented MP2 and PSM at various facilities
Cost Reduction and Efficiency Initiatives
-
Develop line improvement and implement cost reductions on tray pack system resulting in $480,000 savings.
-
Completed Carcass Spray System. Shrink reduced from 2.37% to 0.57% creating a yield gain of $3.0 MM.
-
Completed Stomach Harvesting Line increasing output from 1,000 to 10,500 lbs per day with minimal labor.
-
Completed Bung Harvesting Line increasing output from 500 to 3,250 pounds per day with minimal labor.
-
Examined energy/maintenance operating costs. Implemented vendor/contractor changes to reduce costs.
-
Established standards for floor reconstruction and re-coating contracts to be implemented with vendors.
-
Established facility standards for electrical conduit installation to prevent water related electrical problems.
-
Established tracking and record systems for Work Orders and Facility Projects. New systems allowed the plant to assign limited resources to areas needing the largest impact.
-
Reduced Plant Mechanical Downtime from 3.75% to rate of 1.89%.
-
Reduction of $550,000 in Plant Repair Expenses.
-
Reduced Repair and Maintenance Budget spending by $802,537 after three prior years of overspending.
-
Reduced Equipment Downtime from 3.25% to 2.066% while simultaneously reducing parts spending.
-
Directed energy reduction efforts including capacitors and soft-starts with over $200,000 in annual savings.
-
Implemented Maintenance Parts Fabrication / Alternative Vendor initiative resulting in $171,000 in savings.
-
Directed installation of Tracer Summit Energy Management System.
-
Completed installation of $2.5 MM Auto-Casepack / Auto-Palletize system for four continuous operation wiener lines without any lost production time saving $600,000 annually.
-
Created, developed and implemented casings usage tax reduction project saving $700,000 annually.
-
Completed installation of circulation/recirculation systems on CWP liquid smoke saving $250,000 annually.
-
Design, creation and installation of Main Shipping transfer ramp system resulting in $70,000 labor savings.
Environmental
-
Completed installation of $1.8 MM, 2 MM gal processed waste water aeration, holding / control tank system.
-
Completed improvements for PSM with the Ammonia Refrigeration Systems. Updates included advanced monitoring devices, Enunciator Notification Panel, and new Engine Control Room for refrigeration system monitoring and data collection.
-
Completed $0.5 MM Brine energy reduction / environmental containment project saving $25,000 annually.
-
Reconfigured outdated Waste water system with SS Vertical DAF and equalization saving $125,000 annually.
-
Managed all Environmental Reporting for State and Federal agencies including air, water and waste water.
-
Designed and implemented smoke exhaust opacity controls for Alkar Tunnels in discharge reduction project.
-
Implement MUSCLE computerized maintenance system for the facility.
Projects
-
Replaced two Ammonia IQF Flat Product Freezers over a six month period while keeping the other adjacent lines operating
-
Consolidated two facilities to take advantage of over $1.5 Million in annual savings
-
Completed $3MM Storage Freezer planning and construction project.
-
Completed $3.5 MM Automated Product Transfer and Packaging Project in Fully Cooked Sausage
-
Completed $8 MM Beef Grinding, Freezing and Packaging Utilization and Upgrade Project
-
Completed the design and installation of a new Occupational Health Center for employees.
-
Completed research, design and Engineering for 140 / 180 degree hot water heat exchanger system with back-up capabilities to eliminate downtime caused by the loss of 180 degree water in the plant.
-
Completed installation of Lactic Acid Sanitizing Cabinets for carcasses.
-
Completed installation of the new “Enhanced Pork” production lines.
-
Designed and completed roofing over primary product storage areas to eliminate condensation problems.
-
Completed Loin Boning and Loin Trimming upgrade project to improve yields and production throughput.
-
Completed $2Million, 17,000 sq ft product freezer and 7,000 sq ft refrigerated dock with six shipping doors.
Maintenance Management Systems Used
-
MUSCLE Maintenance Management System
-
GP Mate Maintenance Management System
-
Data Stream Maintenance Management System
-
PMC for Windows from DPSI and UNIX System Program
-
MP2 and Mechanics Mate